Industrial Waste shredder
The XR is an industrial waste shredder for efficient coarse, medium, and fine shredding from a variety of different waste streams. The low-speed, high-torque single-shaft shredder is used to process difficult waste materials such as C&D debris, municipal solid waste (MSW), tires, mattresses, metal scrap, wood waste, and ragger wire. This heavy-duty shredding machine has a production rate of up to 70 tons/hr and allows a defined fraction size from 1" - 12" (25 to 300 mm).
High throughput and maximum availability
Very low operating costs thanks to UNTHA Eco Power Drive
Sturdy machine design
Easy to maintain and service
Driving power: 177 - 2 x 215 hp | 132 - 2 x 160 kW
Rotor diameter: 39.4" | 1,000 mm
Maximum throughput capacity: 70 t / h
Fraction sizes (based on the screen): 1" - 11.8" | 25 - 300 mm
The efficient UNTHA Eco Power Drive is the most efficient design on the market, consuming up to 75% less energy than diesel-powered shredders.
The 7” color touch control panel controls all aspects of the shredder in an easy-to-understand format regardless of operator’s technical abilities.
The XR is built to provide a low-vibration operation in even the most demanding materials to ensure the unit performs at peak efficiency regardless of the waste stream it is asked to process and the end product size required.
The XR waste shredder represents outstanding efficiency, flexibility, and reliability when shredding different material streams.
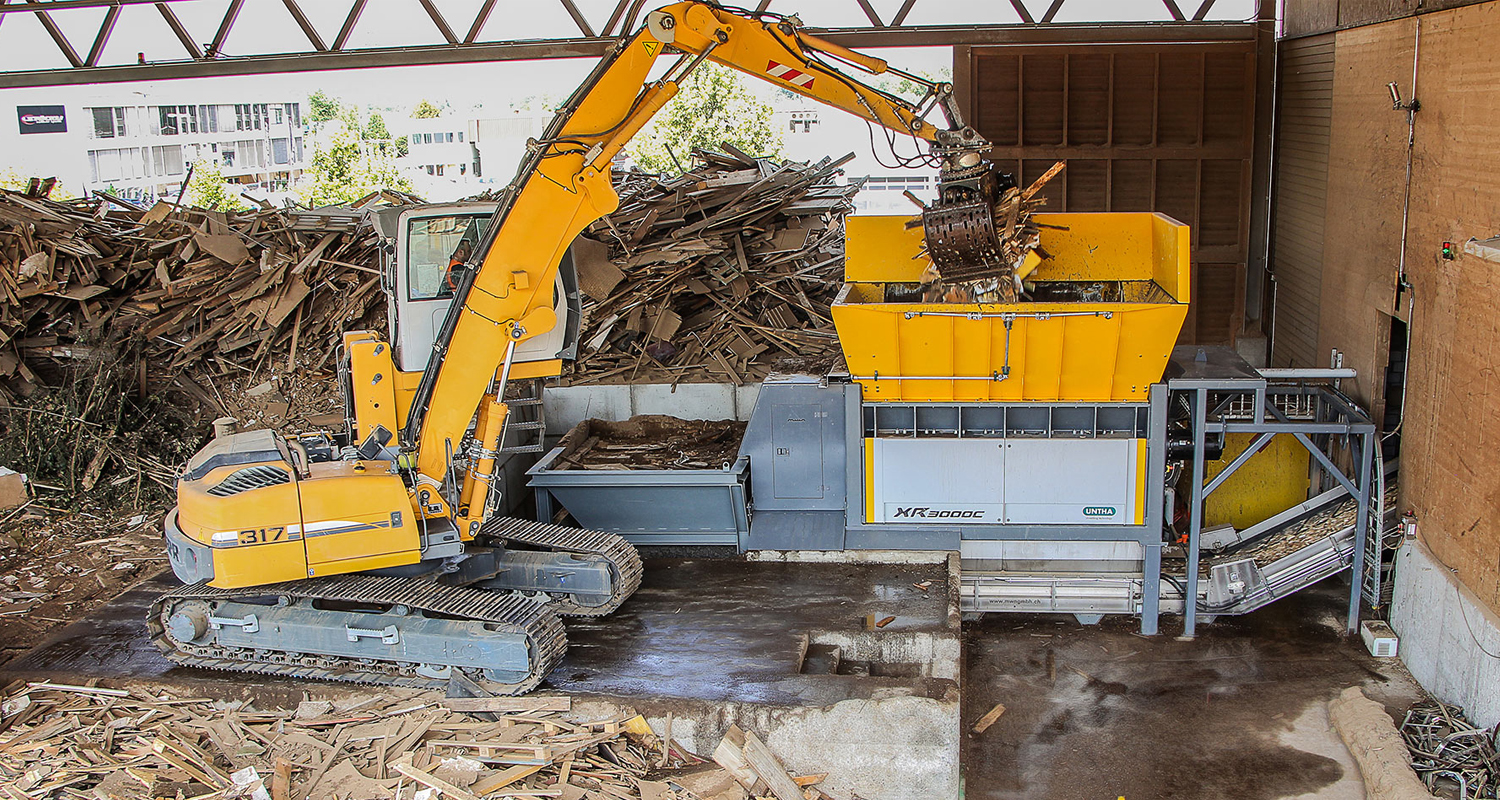
Our low-speed single shaft shredder is used to shred materials such as C&D debris, municipal solid waste (MSW), C&I waste, wood waste, tires, mattresses, metal scrap, and ragger wire. The XR class of shredders can be configured as a primary shredder to process highly contaminated wastes in a single pass or to create a specific sized processed fuel. The machine can be configured with the right rotor, gear box, and screen size to match the machine to the waste stream that needs to be processed.
Depending on the material that needs to be shredded and the sized end product your market demands, the XR can be configured to provide “best in class” performance. The machine can be designed to meet and exceed all of your processing expectations at production rates from 5-70 tph and consistently sized end product anywhere from 5/8” – 12”.
The cutters and counter-knives can be maintained and adjusted easily from outside the machine to maximize the rotor’s ability to process your material. The rotor design and gear box configuration can be customized to allow the shredder to process even the most contaminated waste streams quickly and safely. The XR provides superior resistance to contamination due to the synchronous drive motors and easy access to all critical machine components.
A hydraulically operated panel on the back-side of the rotor allows you to quickly remove any un-shreddable item that makes its way into the rotor to get you back up and running in the shortest amount of time possible.
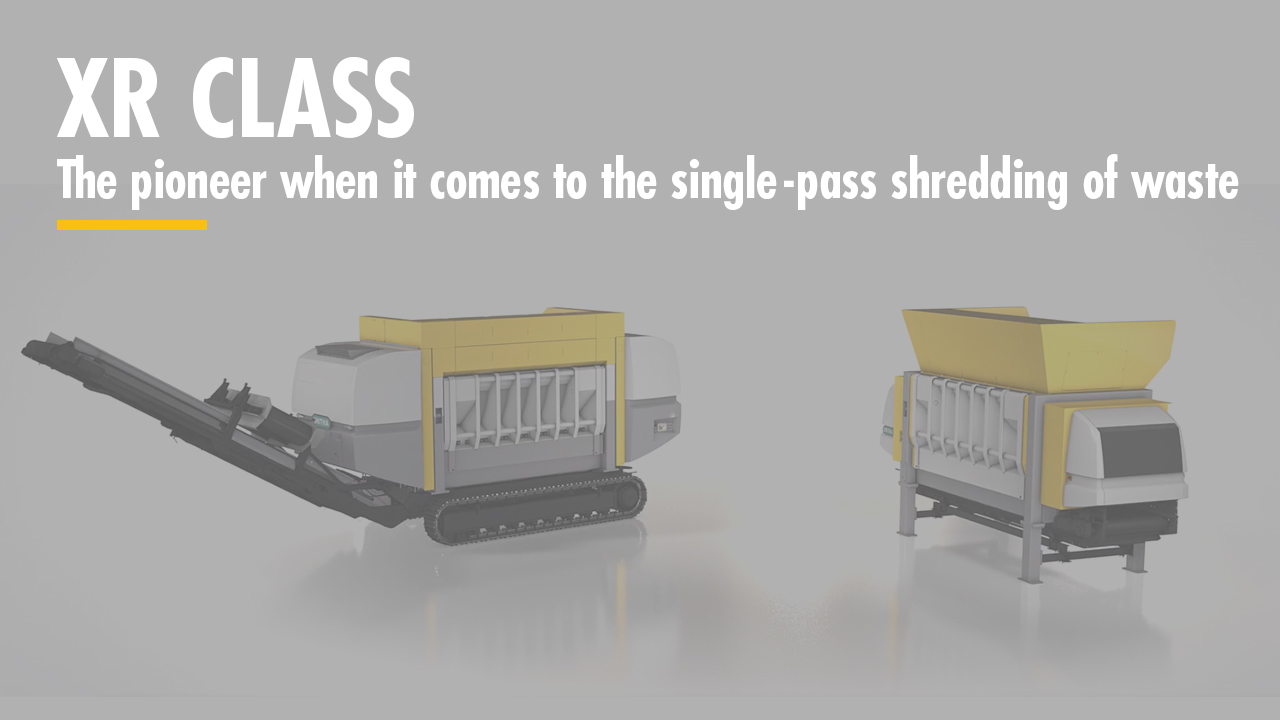
The Stationary XR is a highly efficient single pass shredder for recycling and waste management companies. This unit provides the highest production rates and lowest operating costs on the market because of the UNTHA Eco-Power Drive System. This system uses 30-pole synchronous electric motors direct coupled to the gear box which is mounted inside the rotor for the most efficient, highest torque drive system available.
These motors are water cooled while in operation to provide a 75% lower energy cost as compared to conventional diesel-hydraulic shredders. The direct drive design reduces maintenance costs by eliminating the need for belt drives and stub shafts.
The load sensing speed control ensures the machine is delivering the highest torque available. This coupled with its special solid-steel frame design, high-quality and rugged construction gives this unit the ability to process virtually any waste stream with low vibration and high throughputs.
All aspects of the shredding process were considered while designing this machine to be the most productive and most economical waste shredder on the market today. No facet of the machine design was compromised to ensure we are offering the best technology available in a compact and user friendly design.
These materials can be shredded with the XR2000/3000:
Depending on the material and fraction size, several cutting systems with different blade shapes are available with the RC, C, and XC system. The cutting systems allow fraction sizes from 25 to 300 mm.
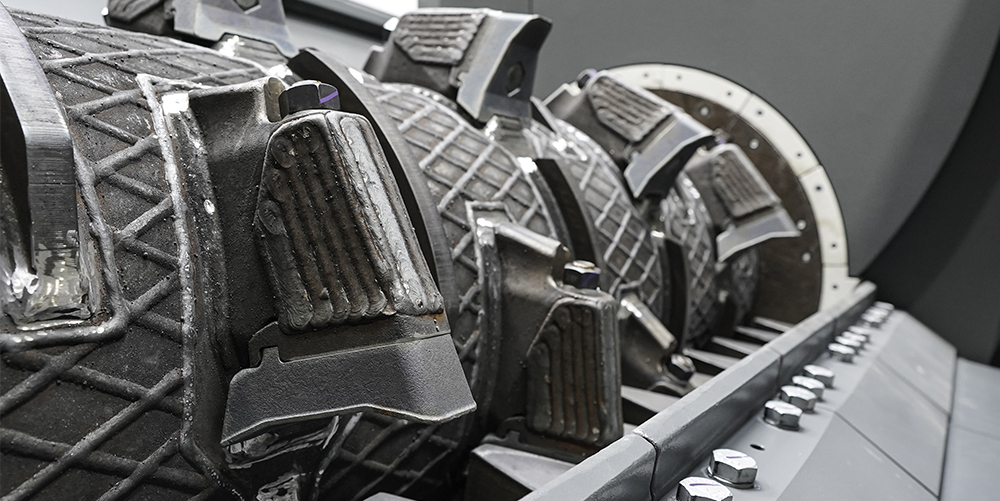
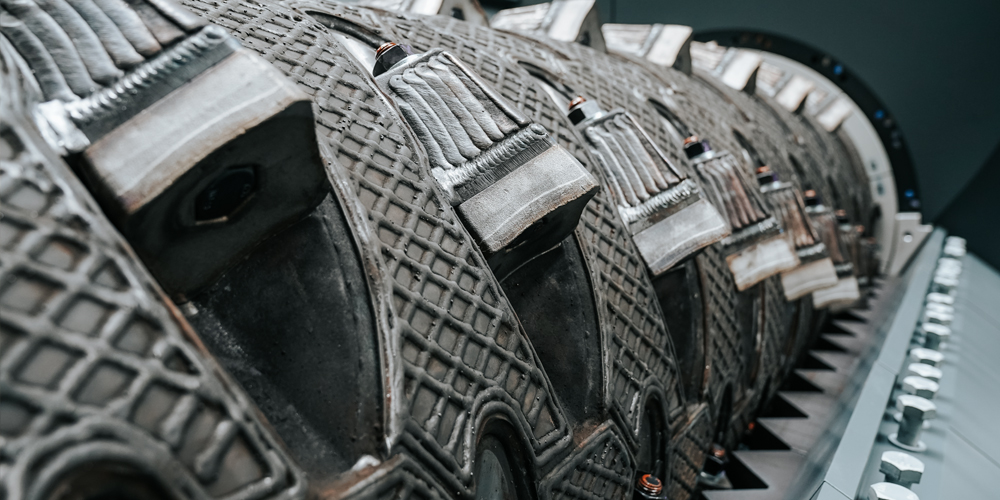
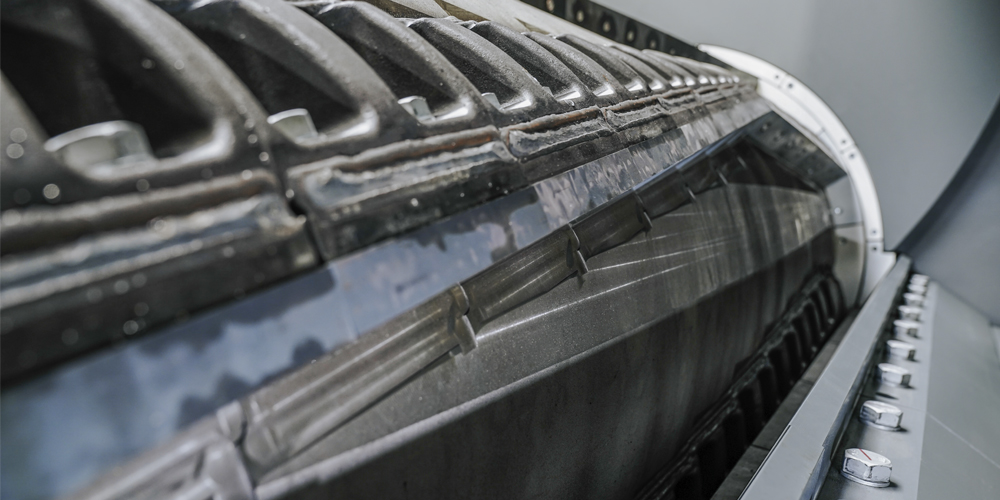
The RC cutting system was specifically developed for the coarse pre-shredding of different material flows and for high throughput rates of up to 70 t/h. The purpose-built shape of the blades ensures a particularly aggressive intake behaviour for the material. The cutters and the stator bar may be welded on again at the end of the service life.
Obtainable fraction sizes: 100 - 300 mm
Thousands of customers from diverse industries around the world already place their trust in the reliable UNTHA name.
The shredder is so flexible that we are able to process not just grade 1 to 3 waste wood, but also grade 4 waste wood. The metal we remove from the wood is sold on to the steel industry.
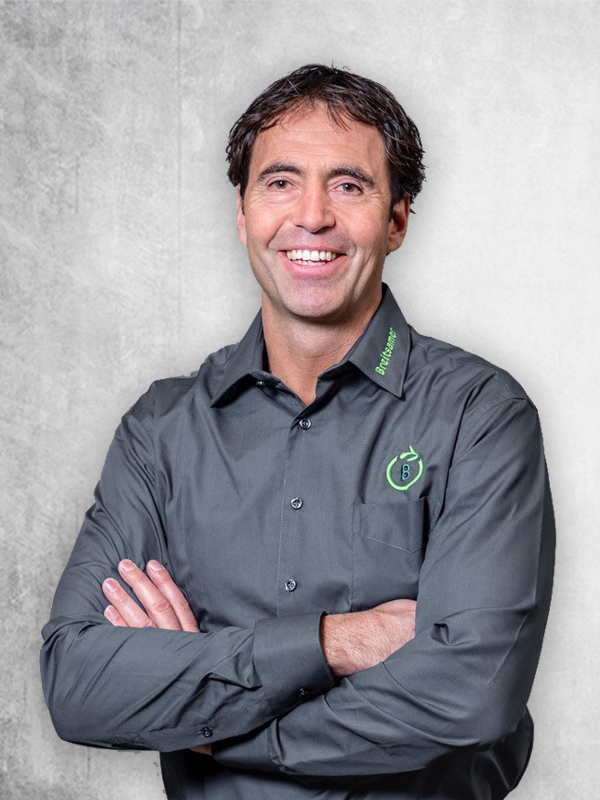
Thomas Breitsamer
Managing Director
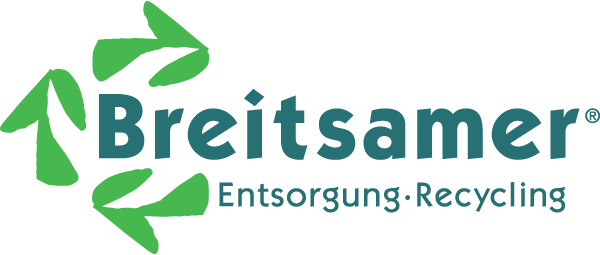
For special requirements, we offer custom-made accessories for this shredder.
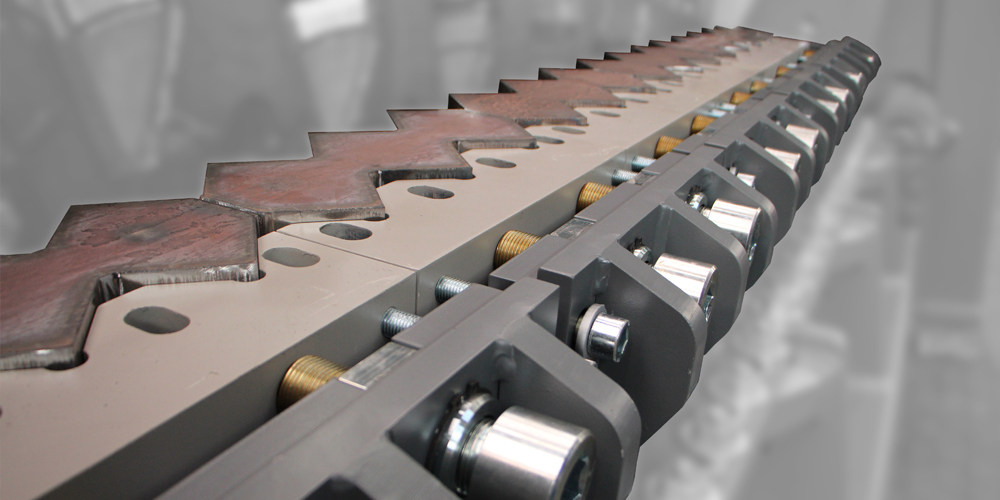
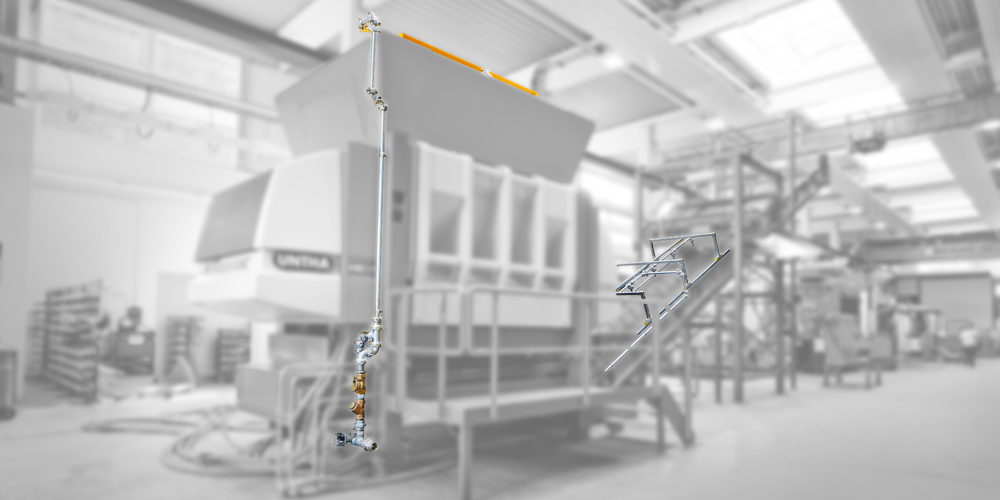
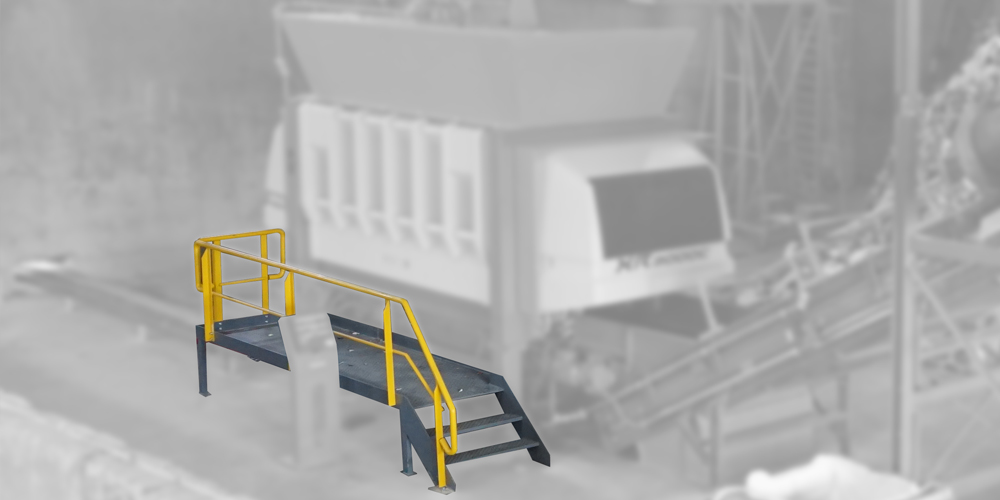
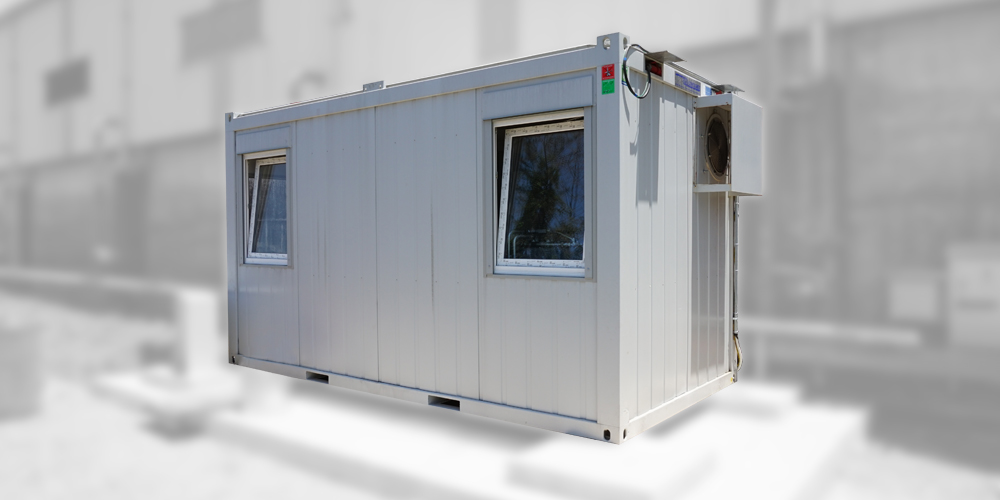
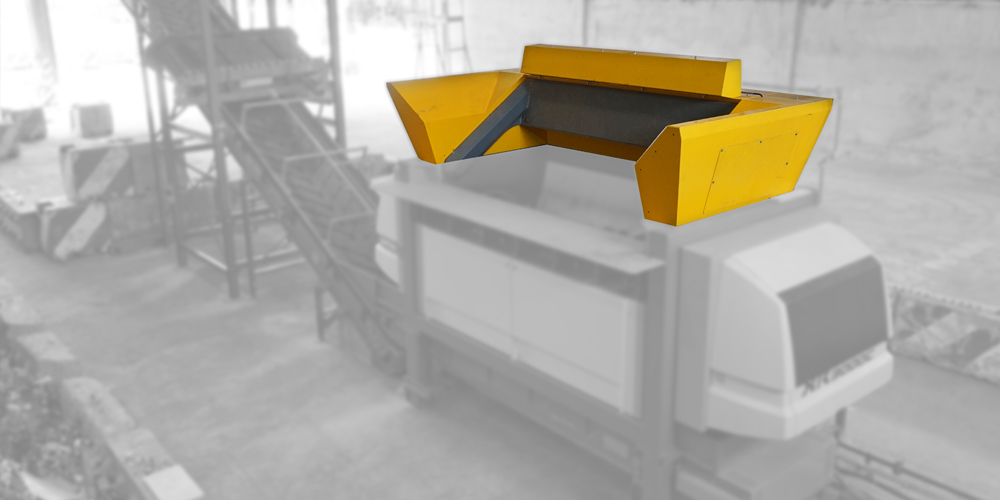
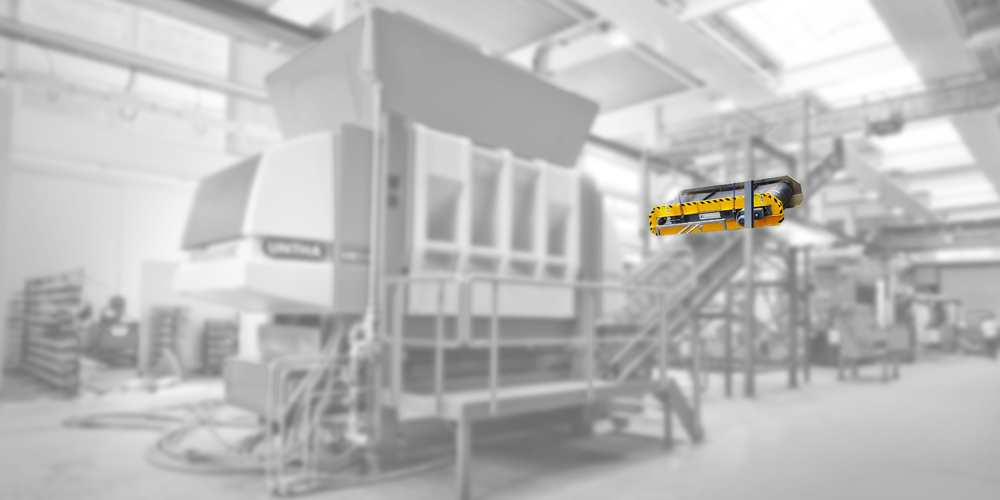
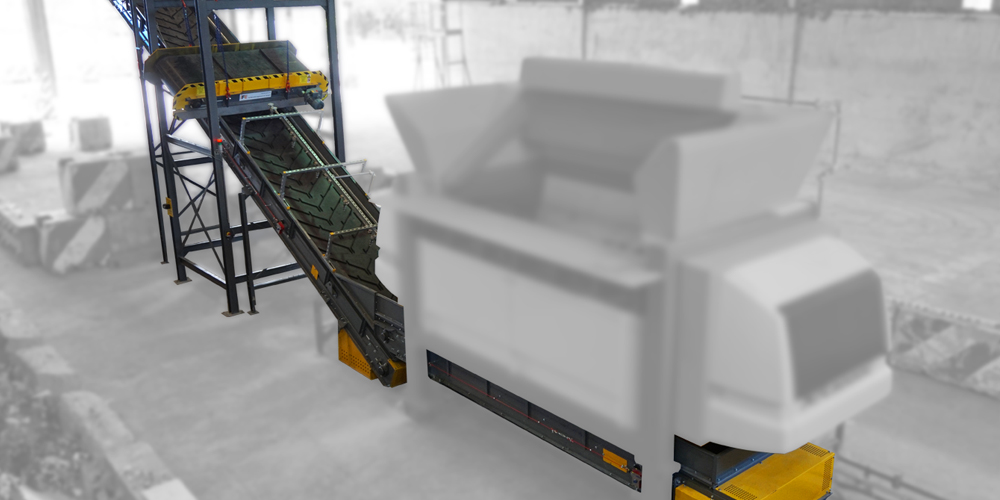
The adjustable main cutting bar offers you the option to adjust the cutting opening. The shredder can be optimally adjusted for the material to be shredded and the required discharge fraction.
This option is only available for the C cutting system.