UNTHA shredding technology scores extra points for quality and flexibility
Recycling specialist Ragg GmbH has invested in a new mobile shredder from UNTHA, as the experienced waste management firm seeks to boost material throughput across its Austrian sites.
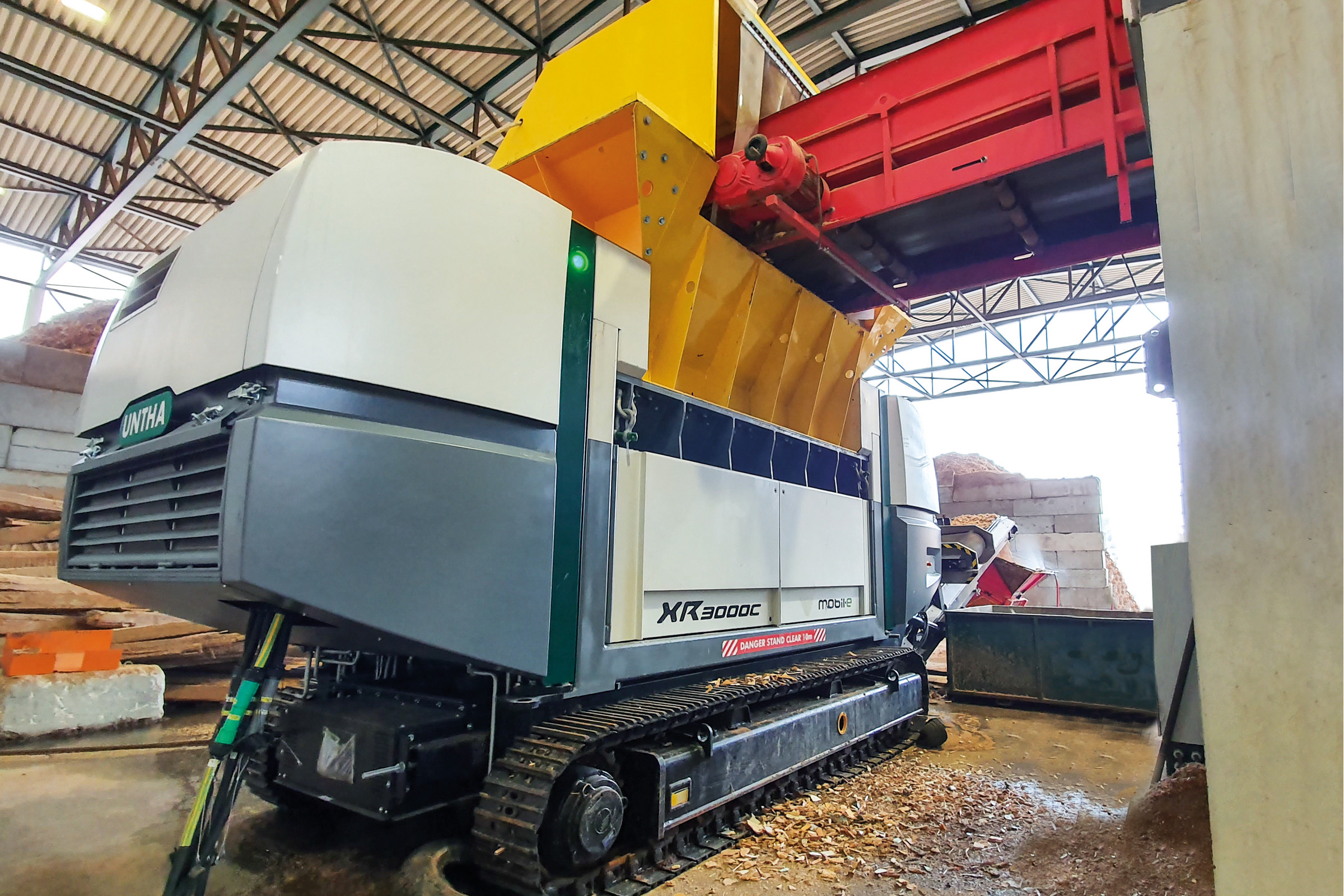
Formed as a small scrap dealership in 1947, Ragg is no stranger to the collection and processing of ‘waste’ for remanufacturing. But fast forward to 2020, and the organisation employs 110 people across four sites, including a timber processing yard in Hall which has been operational since the mid-2000s.
Aware that its incumbent shredding technology was reaching the end of its useful life, operation manager Clemens Gritsch began the search for a new, energy efficient machine to replace Ragg’s existing post-shredding unit.
Impressed with the cost-effective, environmentally-friendly capabilities of UNTHA’s electric drive XR3000C mobil-e, Ragg proceeded to invest in the machine to reduce the fuel consumption and noise levels of the waste processing plant. Reduced wear and increased throughputs have also been added benefits of the new shredding investment. “The fact that the new machine is slow-running, rather than fast-running like our old unit, was an important factor in our decision. The shredding of our input material has improved significantly. In our old unit, we were also using a mobile pre-shredder, which we would operate off-site at times. During those periods, the plant would stand still", explained Clemens.
Now, however, the plant can continue to run as the XR can be fed directly with waste wood. Throughputs of 25-35 tonnes per hour have been achieved, and the XR’s flexible fraction sizing means Ragg can satisfy a range of output specifications ranging from biomass fuels through to chipboard manufacturing materials.
Keen to really put the flexibility of this mobile unit to the test, Ragg will now send the XR ‘on the road’, with Innsbruck the next destination for the waste shredding machine. Here, the technology – with in-built crawler tracks – will be integrated with ease into the plant, to process wider recyclables including rubber. "Energy efficiency, easy accessibility for maintenance and service, and minimal downtime are other benefits that stand out," added Clemens. “For a traditional company like Ragg, we were also pleased that these quality shredders are made right here in Austria.”
This is the second UNTHA machine purchased by Ragg, as an UNTHA RS50 four shaft shredder is also already in operation.
You can also find the whole interview with Clemens Gritsch on Youtube: https://youtu.be/a6NyLR1pcdQ