Cutting-edge development by UNTHA shredding technology:
With the RC cutting system for the XR series, UNTHA has developed an innovative cutter geometry with improved infeed characteristics that enables a high throughput and a highly homogeneous output material. The robust cutting chamber is designed for the pre-shredding of particularly bulky materials and materials with a high content of non-shreddable items.
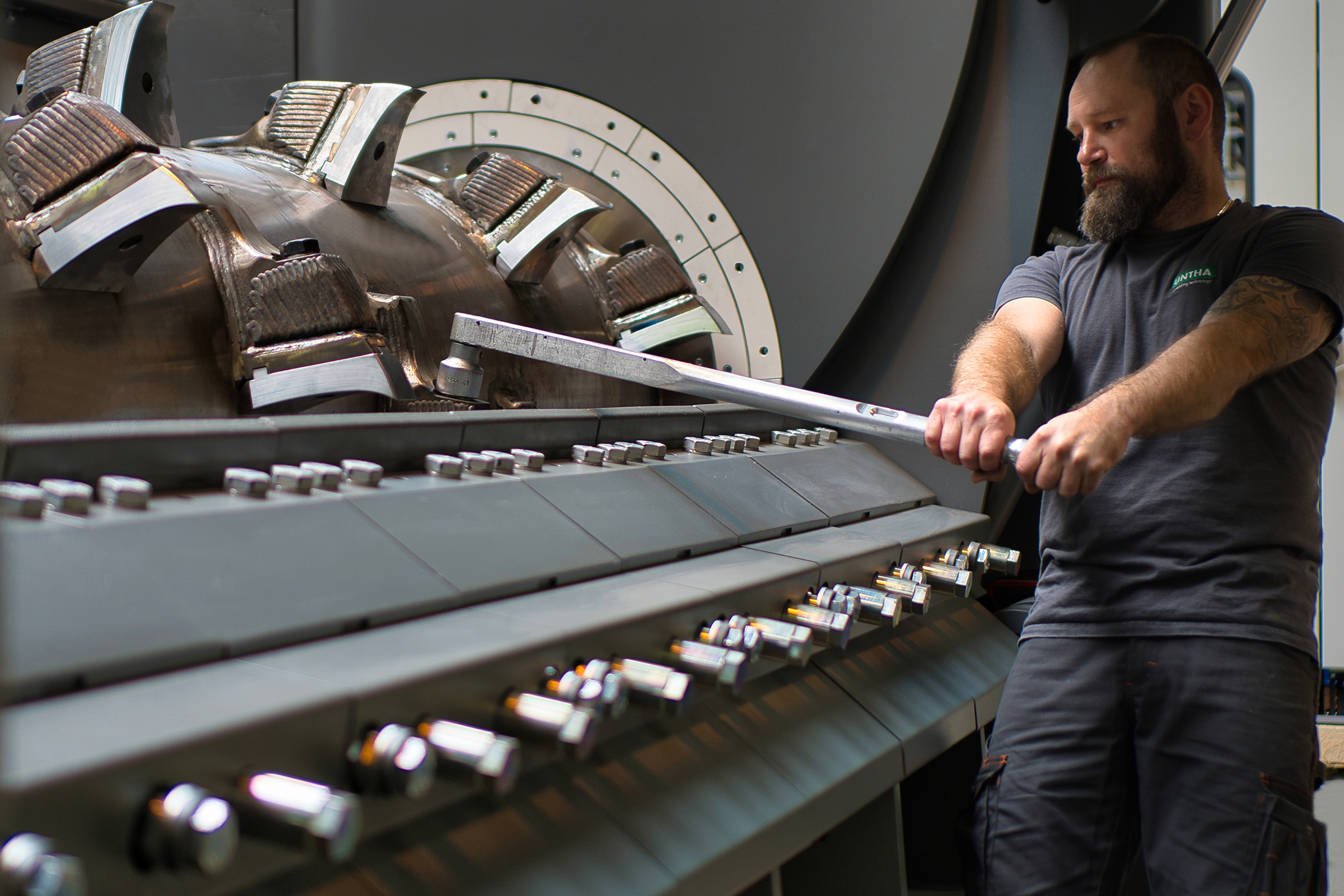
The RC (Ripper Cutter) system stands for the new generation of cutting systems for the XR series, available now as a third option besides the C (Cutter) and the XC (X-Cutter) systems. Following an extensive customer requirement analysis, intense market research and exchanges with potential clients, the new concept of the RC cutting system was developed over a 12-month period. Market research showed a particularly high demand for three criteria, on which the UNTHA development team accordingly focused in its efforts to take the R cutting system to the next level: the elimination of the ram device, resulting in a larger machine opening and depth, reduced maintenance and servicing costs, and optimised value for money. During the field tests using a range of pre-series models, other advantages soon became obvious: The new cutting system with its novel cutter geometry deals with significantly higher throughput volumes of >100 tonnes per hour, for instance of domestic waste. This is equivalent to a performance increase of 50 percent compared to previous systems.
Efficient and flexible
Another advantage is the optimised compatibility with optical sorting devices that results from the low fines content in the output material. This greatly facilitates the downstream processing of the pre-shredded material. The increased efficiency of the cutting system also results in reduced energy consumption. The RC cutting system is used for shredding domestic, bulky and commercial waste as well as waste wood. Depending on individual requirements, the shredder may be equipped with screen bars or a screen. A homogeneous fraction size from 300 to 100 mm in a single step is possible. The shredder may be combined with different drive powers and is available with the energy-saving UNTHA Eco Power Drive or the high-performance UNTHA Power Drive. “The real challenge in the development of the RC cutting system was to reach a level of robustness that deals with all types of non-shreddables. Thanks to the unique shape of the teeth, the system is particularly resilient,” explains Christian Lanner, Head of Technology & Innovation at UNTHA shredding technology.
Longer lifespan due to weld-on concept
To keep maintenance and servicing costs to a minimum, UNTHA has developed a particular weld-on concept for the RC cutting system. Operators of the XR shredder may weld on the cutters and the stator bar themselves at the end of the service life or have this done by the UNTHA service engineers.
XR on tour
Customers are already impressed by the performance standards of the new RC cutting system. Even during the early testing phase, three orders were placed with UNTHA. For all interested parties, an XR demo unit is currently on tour to demonstrate the benefits of the new cutting system on a range of materials directly at operators’ sites.